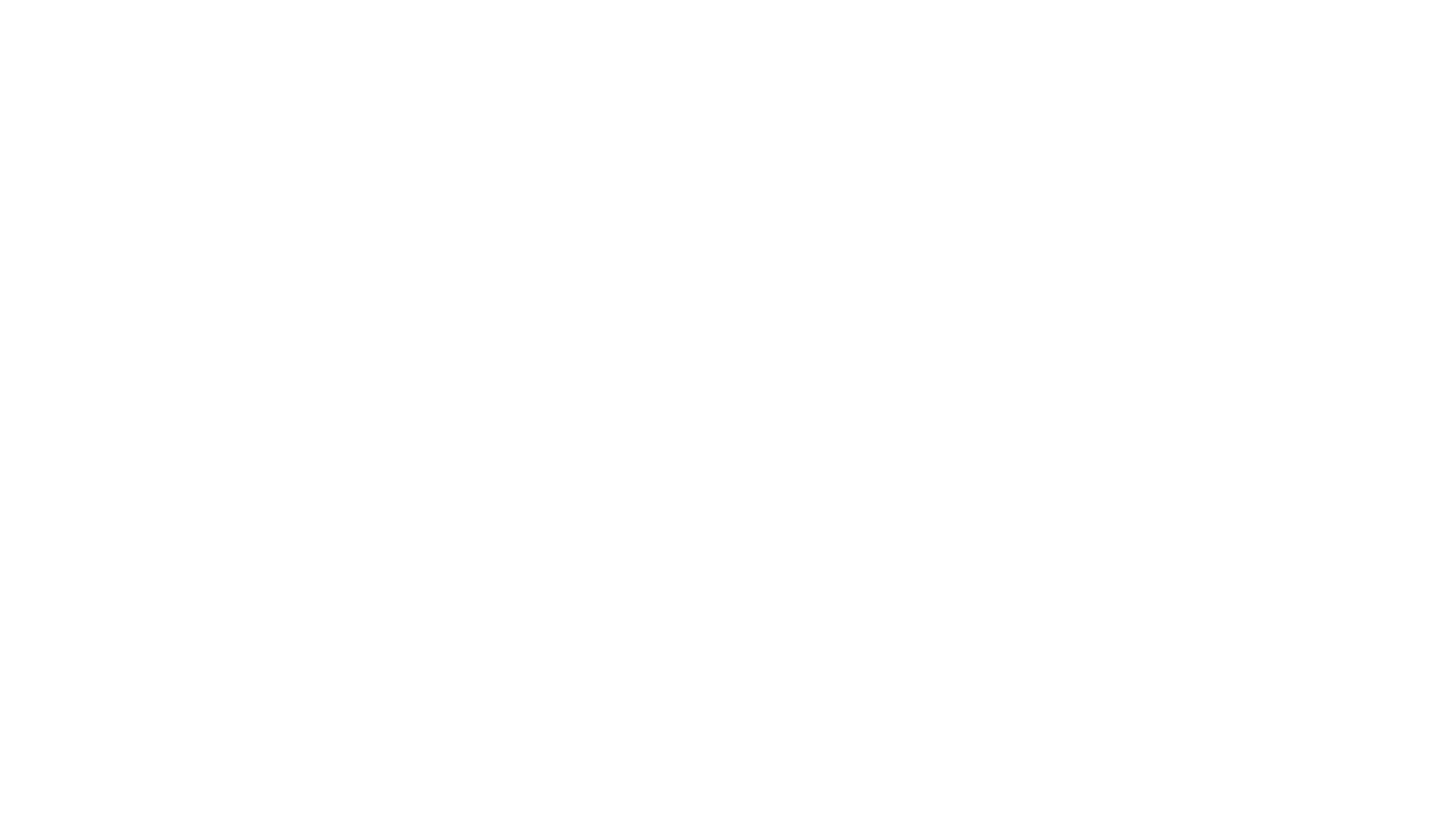
April 18, 2023
Introduction:
Blown film is a popular plastic film manufacturing process used to create a variety of products, from food packaging to construction materials. The process involves extruding molten plastic through a circular die, inflating it with air to create a bubble, and then cooling and flattening it into a film. However, the quality of the final product is heavily dependent on the precision of the manufacturing process, which requires careful monitoring and control of several parameters. This article will explore the blown film manufacturing process in detail and discuss the importance of process control measures in ensuring high-quality, consistent products.
Blown Film Manufacturing Process:
The blown film process involves several steps, each of which requires precise control to ensure the desired product properties. First, the plastic resin is fed into an extruder, where it is heated and melted. The melted plastic is then forced through a circular die, which shapes it into a tube. As the tube exits the die, it is inflated with air, creating a bubble. The bubble is then stretched and cooled by passing it through a series of rollers, which flatten it into a film of the desired thickness and width. Finally, the film is wound onto a roll for storage and transport.
Process Control Measures: To ensure the quality and consistency of the final product, several process control measures must be implemented throughout the blown film manufacturing process. These include:
-
Raw Material Quality Control: The quality of the plastic resin used in the blown film process can have a significant impact on the final product. Therefore, it is essential to test the resin for purity, melt flow rate, and other key properties before use.
-
Temperature Control: The temperature of the extruder and die must be precisely controlled to ensure the plastic melts uniformly and flows smoothly through the die. Any deviations in temperature can result in defects such as melt fracture or die lines.
-
Air Pressure Control: The air pressure used to inflate the bubble must be carefully controlled to ensure consistent bubble size and thickness. Deviations in air pressure can lead to uneven film thickness or even bubble burst.
-
Cooling Control: The cooling process must be carefully controlled to ensure the film cools evenly and uniformly, without any hot or cold spots. Any deviation can result in warping or distortion of the film.
-
Winding Tension Control: The winding tension must be carefully controlled to prevent stretching or tearing of the film during winding. This can result in uneven film thickness or even film breakage.
Conclusion:
Blown film manufacturing is a complex process that requires precise control and monitoring to ensure high-quality, consistent products. Process control measures such as raw material quality control, temperature control, air pressure control, cooling control, and winding tension control are essential to ensure that the final product meets the desired specifications. By implementing these measures, blown film manufacturers can produce high-quality products that meet the needs of their customers and satisfy the demands of the market.
The blown film process involves several steps, each of which requires precise control to ensure the desired product properties
“
Discover our measurement solutions for the BLOWN FILM manufacturing process.
Related Articles
Enhancing Aseptic Package Production
Optimize aseptic package production with Scantech’s advanced measurement solutions. Improve quality, productivity, and safety.
How to Calculate Density: Formulas, Examples, and Practical Tips
Density is a fundamental concept encountered in numerous fields of science and engineering, ranging from materials science.
Online Non-Contact Measurement: The Ideal Solution for Precise and Contact-Free Measurements
In a world where efficiency and precision are essential, Online Non-Contact Measurement has become a must-have solution for many industries.