EXTRUSION
MEASUREMENT SYSTEM FOR
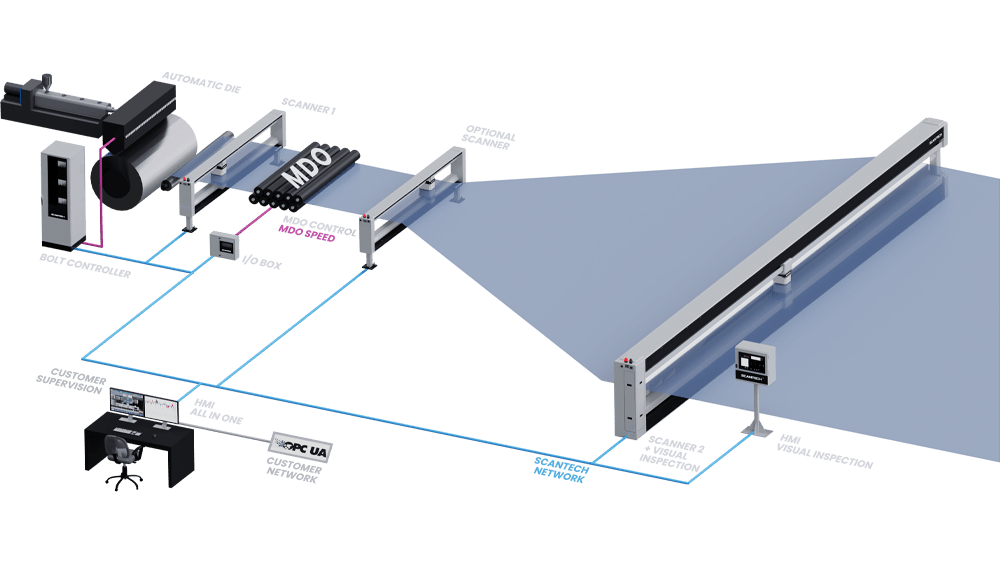
BIAX FILMS
BOPP, BOPE, BOPET, BOPA, BPPS, BOPI…
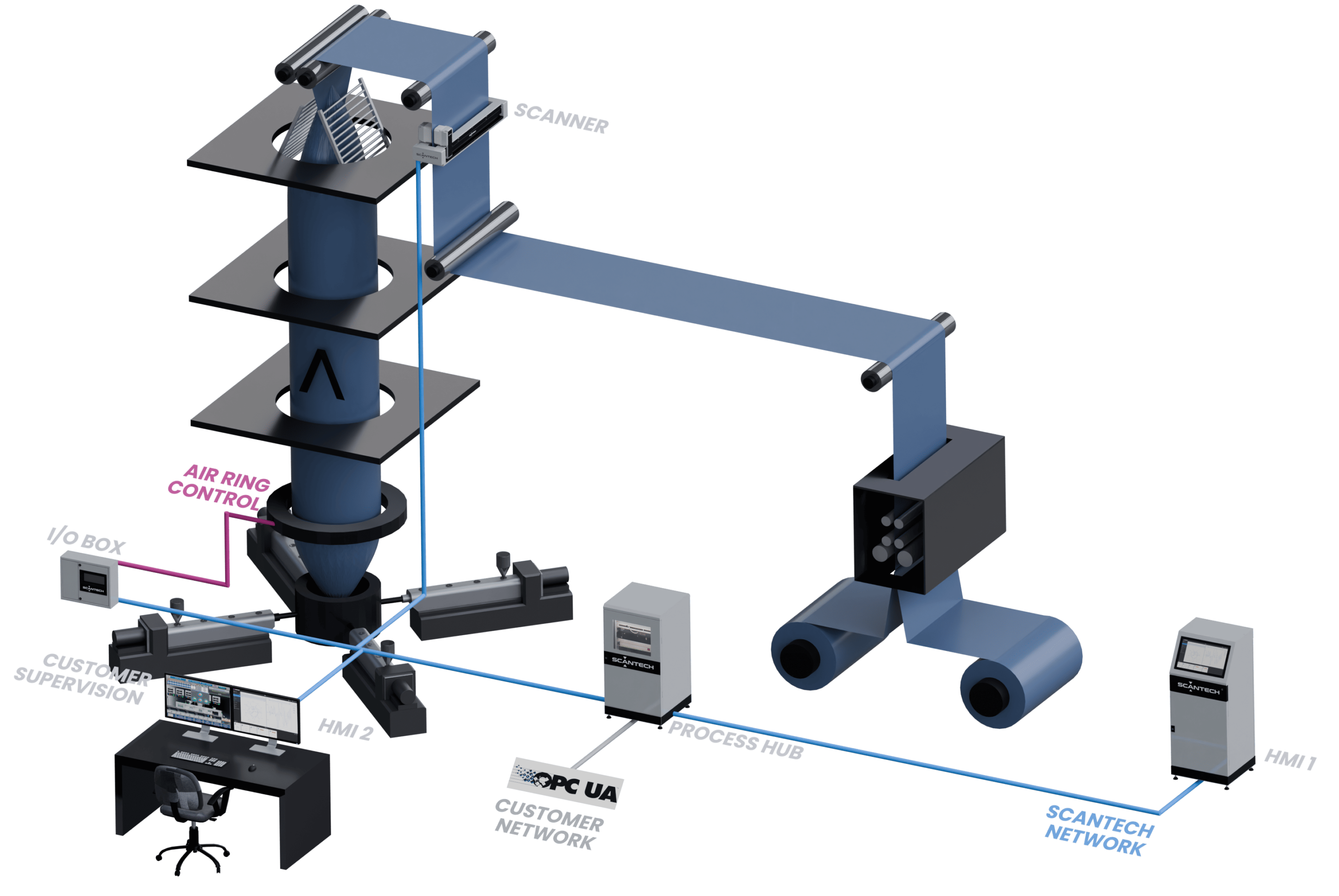
BLOWN FILMS
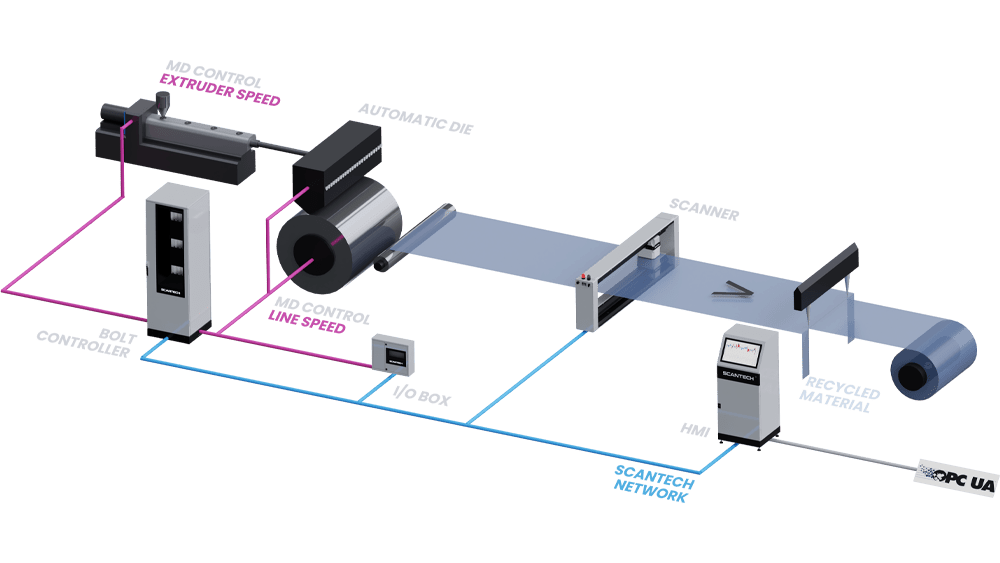
CAST FILMS & SHEET
CPP, CPE, Barrier films…
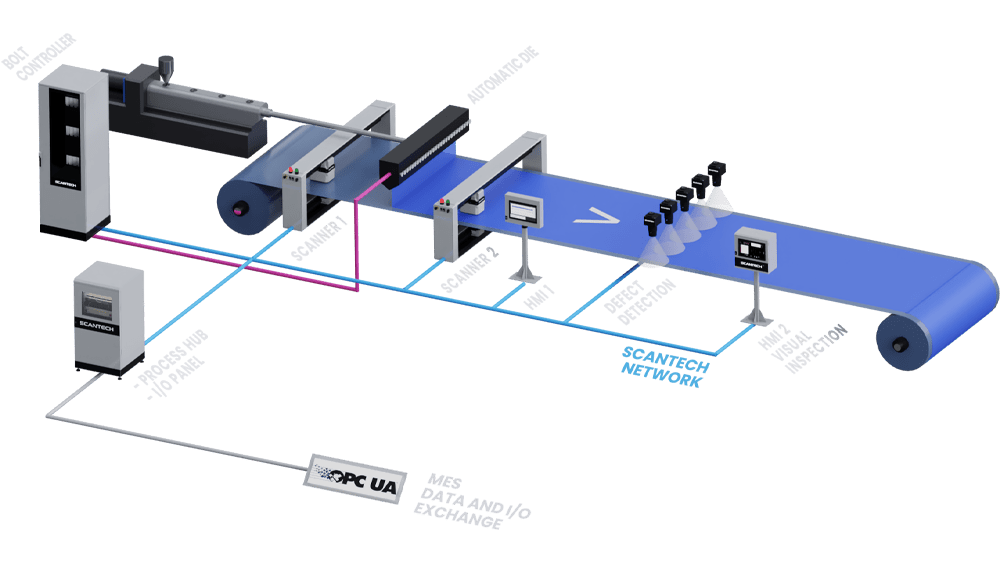
COATING FILMS
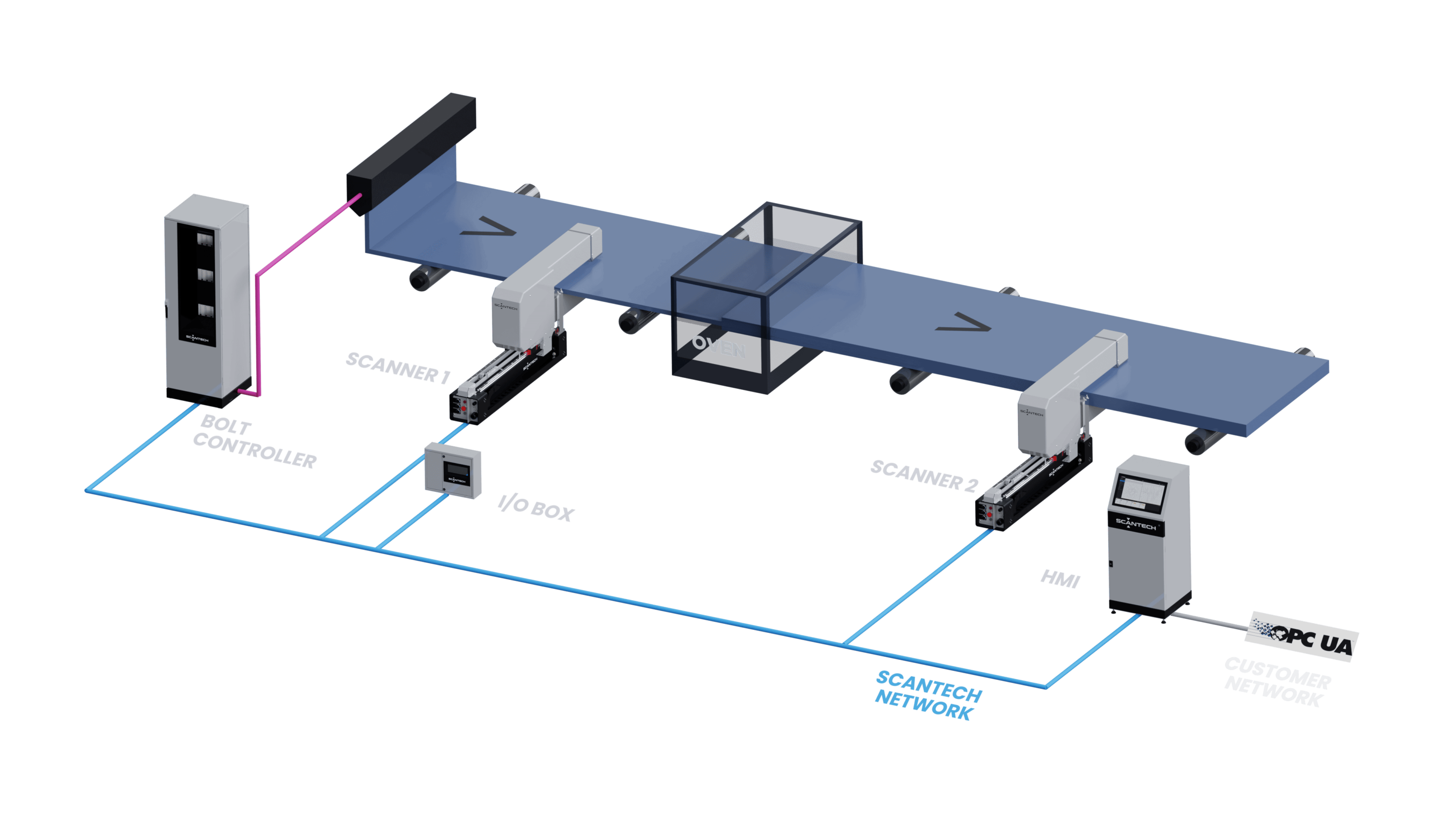
FOAMS
PU, PET…
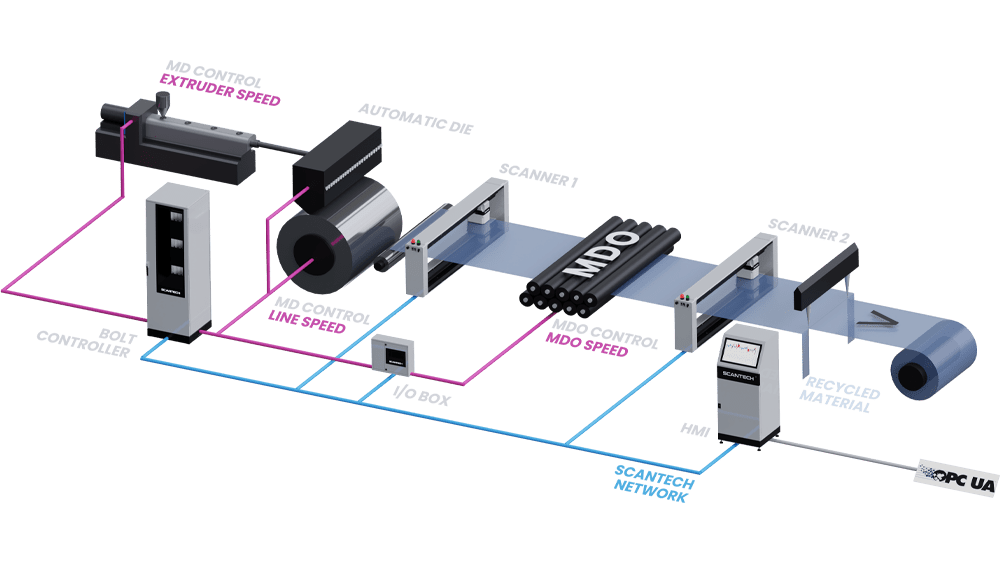
MDO FILMS
MDPP, MDPE…
Extrusion is a manufacturing process used to create objects with a uniform cross-section. In the extrusion industry, accurate measurement is critical to ensuring product quality and consistency. But what is the measurement system used in extrusion, and how does it impact quality control?
Accurate measurement in extrusion is essential to ensure that the finished product meets the desired specifications. The extrusion process involves pushing material through a die to create a specific shape or profile. Even slight variations in measurement can result in significant differences in the final product, affecting its performance and reliability.
There are different types of measurement systems used in extrusion, including dimensional, temperature, and pressure measurement systems. Dimensional measurement systems help ensure that the finished product has the correct dimensions and geometry, while temperature and pressure measurement systems ensure that the material is within the correct temperature and pressure range for the extrusion process.
Measurement systems play a crucial role in quality control in extrusion. By monitoring the dimensions, temperature, and pressure during the extrusion process, manufacturers can ensure that the finished product meets the desired specifications. This, in turn, helps reduce waste, lower production costs, and increase customer satisfaction.
In conclusion, accurate measurement is essential in the extrusion industry to ensure product quality and consistency. By understanding the different measurement systems used in extrusion and their importance in quality control, manufacturers can improve their production processes and meet customer demands.