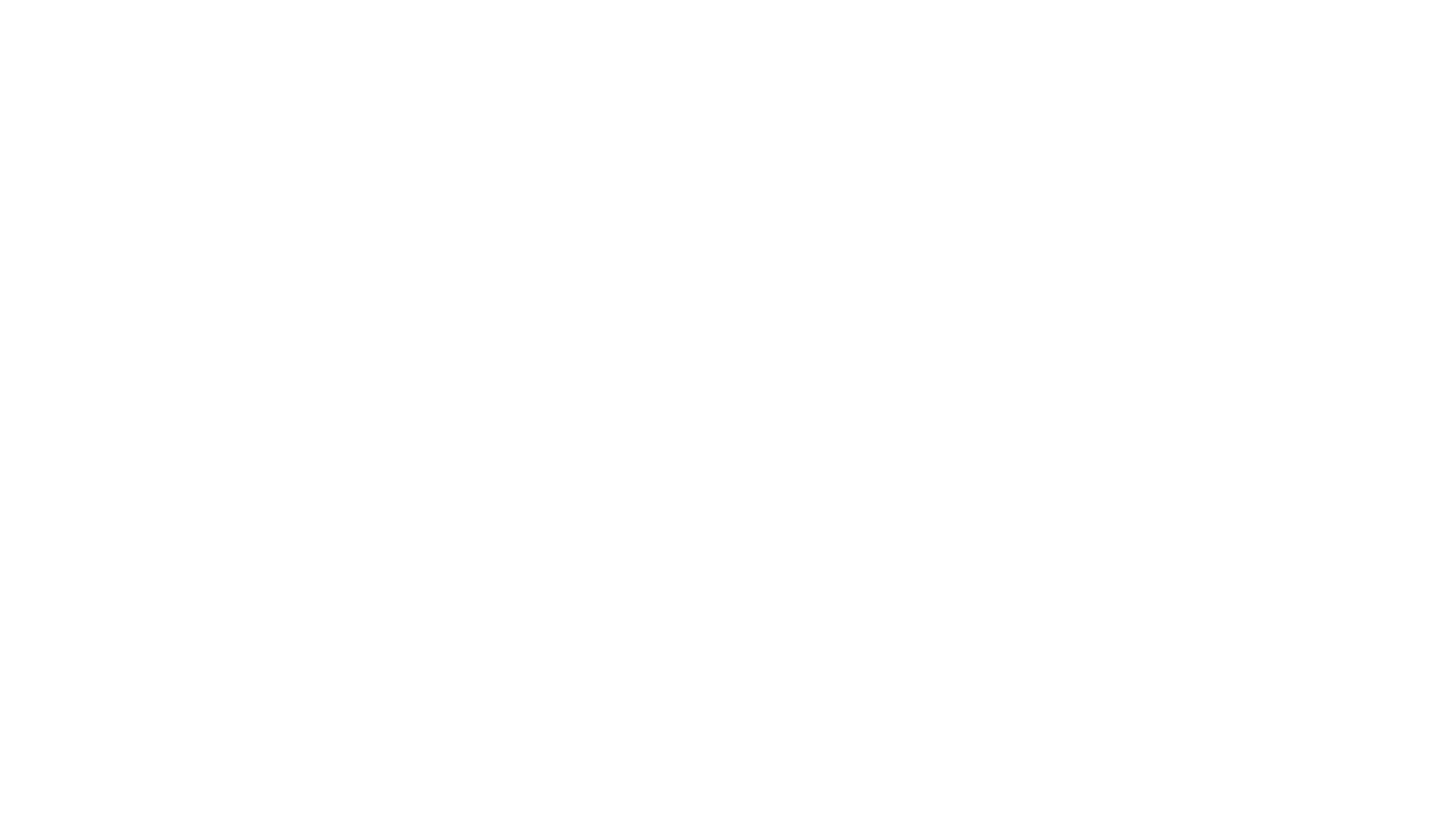
February 4, 2025
Introduction: Understanding Packaging Technologies
Packaging plays a crucial role in preserving the quality and safety of perishable products. Two primary technologies dominate the industry: aseptic packaging and chilled packaging. While both aim to maintain product freshness, they differ significantly in their material composition, processing methods, and storage requirements.
What Is Aseptic Packaging?
Aseptic packaging is designed to keep products sterile and shelf-stable without refrigeration. This is achieved through a combination of sterilized packaging material and aseptic filling processes.
Material Composition of Aseptic Packaging
Aseptic packaging consists of multiple barrier layers, each serving a specific function:
• Outer Paper Layer: Provides rigidity and a printable surface.
• Polyethylene (PE) Layers: Ensure sealing integrity and moisture resistance.
• Aluminum Foil Layer: Acts as a complete barrier against oxygen, light, and contaminants.
• Inner Polyethylene Layer: Forms a food-safe contact surface.
Key Characteristics of Aseptic Packaging:
✅ No refrigeration required – Products remain stable at ambient temperature.
✅ Long shelf life – Typically 6 to 12 months without preservatives.
✅ Sterility ensured – Packaging and contents are sterilized separately before sealing.
✅ Applications – Used for milk, fruit juices, soups, pharmaceutical products, and more.
What Is Chilled Packaging?
Chilled packaging, also known as refrigerated packaging, is designed for products that require constant low temperatures to maintain freshness and safety. Unlike aseptic packaging, chilled packaging does not involve sterilization—instead, it relies on the cold chain to prevent bacterial growth.
Material Composition of Chilled Packaging
Chilled packaging materials are optimized for moisture control and mechanical strength rather than sterility:
• Polyethylene (PE) or Polypropylene (PP) Layers: Provide moisture resistance.
• EVOH (Ethylene Vinyl Alcohol) Barrier Layer: Prevents oxygen penetration, reducing spoilage.
• Paperboard or PET Layers: Offer mechanical protection and branding surfaces.
Key Characteristics of Chilled Packaging:
✅ Requires refrigeration – Stored at temperatures between 0°C and 5°C.
✅ Shorter shelf life – Ranges from a few days to weeks.
✅ Less complex processing – No need for high-temperature sterilization.
✅ Applications – Common for fresh dairy products, meats, salads, and fresh juices.
Key Differences: Aseptic vs. Chilled Packaging
Feature Aseptic Packaging Chilled Packaging
Sterilization Yes, packaging and content are sterilized separately No sterilization, refrigeration prevents spoilage
Storage Conditions Room temperature (ambient) Requires refrigeration (0-5°C)
Shelf Life 6-12 months (without preservatives) Few days to weeks
Barrier Materials Paper, PE, aluminum foil Paperboard, PE, EVOH, PET
Applications Juices, UHT milk, soups, pharmaceuticals Fresh milk, meats, salads, fresh juices
Optimizing Packaging Production with Scantech
Regardless of the packaging type, precision in material composition and thickness is essential for maintaining quality, safety, and cost-efficiency.
Traditional measurement systems often rely on beta radiation sources, which pose regulatory and safety challenges. Scantech’s advanced non-nuclear measurement solutions offer a safer, more efficient alternative for real-time quality control in both aseptic and chilled packaging production.
Why Choose Scantech for Packaging Measurement?
✅ Superior accuracy in multilayer packaging thickness control.
✅ Non-radioactive technology for a safer, regulatory-free process.
✅ Improved productivity with real-time process adjustments.
✅ Cost-effective solution with reduced waste and compliance costs.
Conclusion
Aseptic and chilled packaging materials serve different roles in food and beverage preservation. While aseptic packagingensures long shelf life without refrigeration, chilled packaging maintains freshness under cold conditions.
To optimize production and enhance packaging performance, manufacturers must ensure precise material control. With Scantech’s cutting-edge measurement solutions, industries can achieve the highest standards in packaging quality, safety, and efficiency.
Upgrade your production process today with Scantech’s advanced measurement technology. Contact us to learn more!
Learn more about our online non-contact measurement solutions!
“
Discover our measurement solutions
Related Articles
How to Calculate Density: Formulas, Examples, and Practical Tips
Density is a fundamental concept encountered in numerous fields of science and engineering, ranging from materials science.
Online Non-Contact Measurement: The Ideal Solution for Precise and Contact-Free Measurements
In a world where efficiency and precision are essential, Online Non-Contact Measurement has become a must-have solution for many industries.
Auto-Calibration, Safe & Accurate
BLOWN FILM SCANNERS VIDEO